Under current competitive environment, mold manufacturers should not only can make mold, but also can figure out various problems came up with by customers, such as shrinkage, mold temperature, heating temperature ate and other methods of demolding. With the application of pressure sensor, injection mold manufacturers can have the ability to figure out problems.
The pressure sensor can be installed at nozzle, hot runner and cold runner of injection molding machine or cavity of mold. It can measure pressure of plastic from nozzle of injection molding machine to somewhere in cavity during injection molding, mold filling, pressure maintaining and cooling. The data can be recorded in monitoring system, which are used to adjust pressure of molding in time and inspect or eliminate obstacles during production after molding. It is worth mentioning that collected data can be used as universal technological parameters for the mold or materials. In other words, the data can be used on different injection molding machines if they are using the same mold.
Nowadays, pressure sensor used in cavity is classified into two types, paperback and indirect. Paperback pressure sensor is inserted into cavity through a mounting hole drilled on the back of cavity. The top of pressure comes all the way up to surface of cavity. Cables cross through mold and connect with interfaces of monitoring system on the outside surface of mold. The advantage of sensor is that it cannot be disturbed by pressure during demolding. And it can be damaged easily under high temperature, difficult for installing.
Indirect sensor is classified into sliding sensor and button senor. Both of them are the sensor transmitting pressure on ejector or steady pin applied by plastic melt to senor on ejector plate or moving plate of mold. Sliding sensor is usually installed on ejector plate under pushing pin. When carry out high temperature injection molding or use low pressure senor for small lifting pin, sliding sensor is generally installed on moving plate of mold. Then, pushing pin work through ejector sleeve or using other transition pin. The transition pin has two functions. One is that it can prevent sliding sensor from being disturbed by demolding pressure under the situation of using ejector. The other is that it can protect sensor from being influenced by high acceleration and deceleration of ejector plate for short production cycle and high demolding speed.
The dimension of pushing pin on the top of sliding sensor decides the dimension of required sensor. When cavity needs to be installed with various sensors, mold designers have better to use the same lifting pin in case of setup errors or adjustment errors. The ejector pin is used to transmit pressure of plastic melt to sensor. For this, different products require lifting pin having different dimensions.
In general, button sensor is fixed inside mold. Installation site of senor must be the position that processing personnel is the most interested. If tear down the sensor, template must be opened or particular design is carried out on structure in advance.
Based on different position of button pressure, set box of cables may be installed on template. Compared with sliding sensor, the reading of button sensor is more reliable. This is due to that button sensor is always fixed in slot of mold, different from sliding sensor which moves inside drill hole. So, button sensor should be adopted as much as possible.
The pressure sensor can be installed at nozzle, hot runner and cold runner of injection molding machine or cavity of mold. It can measure pressure of plastic from nozzle of injection molding machine to somewhere in cavity during injection molding, mold filling, pressure maintaining and cooling. The data can be recorded in monitoring system, which are used to adjust pressure of molding in time and inspect or eliminate obstacles during production after molding. It is worth mentioning that collected data can be used as universal technological parameters for the mold or materials. In other words, the data can be used on different injection molding machines if they are using the same mold.
Nowadays, pressure sensor used in cavity is classified into two types, paperback and indirect. Paperback pressure sensor is inserted into cavity through a mounting hole drilled on the back of cavity. The top of pressure comes all the way up to surface of cavity. Cables cross through mold and connect with interfaces of monitoring system on the outside surface of mold. The advantage of sensor is that it cannot be disturbed by pressure during demolding. And it can be damaged easily under high temperature, difficult for installing.
Indirect sensor is classified into sliding sensor and button senor. Both of them are the sensor transmitting pressure on ejector or steady pin applied by plastic melt to senor on ejector plate or moving plate of mold. Sliding sensor is usually installed on ejector plate under pushing pin. When carry out high temperature injection molding or use low pressure senor for small lifting pin, sliding sensor is generally installed on moving plate of mold. Then, pushing pin work through ejector sleeve or using other transition pin. The transition pin has two functions. One is that it can prevent sliding sensor from being disturbed by demolding pressure under the situation of using ejector. The other is that it can protect sensor from being influenced by high acceleration and deceleration of ejector plate for short production cycle and high demolding speed.
The dimension of pushing pin on the top of sliding sensor decides the dimension of required sensor. When cavity needs to be installed with various sensors, mold designers have better to use the same lifting pin in case of setup errors or adjustment errors. The ejector pin is used to transmit pressure of plastic melt to sensor. For this, different products require lifting pin having different dimensions.
In general, button sensor is fixed inside mold. Installation site of senor must be the position that processing personnel is the most interested. If tear down the sensor, template must be opened or particular design is carried out on structure in advance.
Based on different position of button pressure, set box of cables may be installed on template. Compared with sliding sensor, the reading of button sensor is more reliable. This is due to that button sensor is always fixed in slot of mold, different from sliding sensor which moves inside drill hole. So, button sensor should be adopted as much as possible.
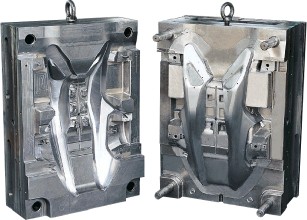