1. There is a layer of compact surface layer on the surface of die castings, and thickness is about 0.05~0.1mm. Substratum is loose poriferous structure. Therefore, during polishing, the surface cannot be polished completely and expose loose substratum. Otherwise, electroplating will be very difficult and it will weaken corrosion resistance of alloy.
2. Die castings change from molten state to solid state during die casting. Due to the different freezing points during freezing, segregation is usually caused on the surface of die castings, making parts of surface cause aluminum-rich phase and zinc-rich phase. So, during pretreatment, strong base and strong acid should not be used to deoil and etching, because strong base firstly dissolve aluminum-rich and strong acid firstly dissolve zinc-rich so that pinhole and micro-pores are formed on the surface of die castings. In addition, strong base and strong acid are remained which easily result in decrustation and bubbles after plating cladding layer.
3. The shape of zinc alloy die casting is commonly quite complicated. Electroplating should use solution having good dispersing power and covering power. To prevent positive metal replacement of potential from occurring in recession and shelter, making poor binding force, pre-plating layer should even more choose plating solution having good dispersing power and covering power.
4. Used plating layer had better be light plating layer to avoid polishing or reduce workload of polishing as much as possible. On the one hand, for complicated shape, die castings are not easy for polishing, on the other hand, the thickness of plating layer can be maintained so that quality can be ensured.
5. If the first plating layer uses copper layer, the thickness should be thicker. Because when copper is plated on the surface of zinc alloy, the thinner copper layer is, the more quick diffusion is, so the thickness of copper should reach to 7 μm at least or thicker.
6. Multi-layer plating chromium is cathode protective coating of zinc alloy, so the layer should have definite thickness, ensuring that there are no pores existing in coating. The electrode potential of zinc alloy is negative, it can easily produce white power corrosion products of zinc carbonate in moist air. Nevertheless, appropriate thickness of layer must be chosen based on using conditions of products.
7. If die casting technology is inappropriate or design of die casting mold is unreasonable, causing cold shuts, shrinkage cavity, loosen or pinholes on the surface of die castings, even take measures on electroplating technologies, qualified layer cannot be acquired.
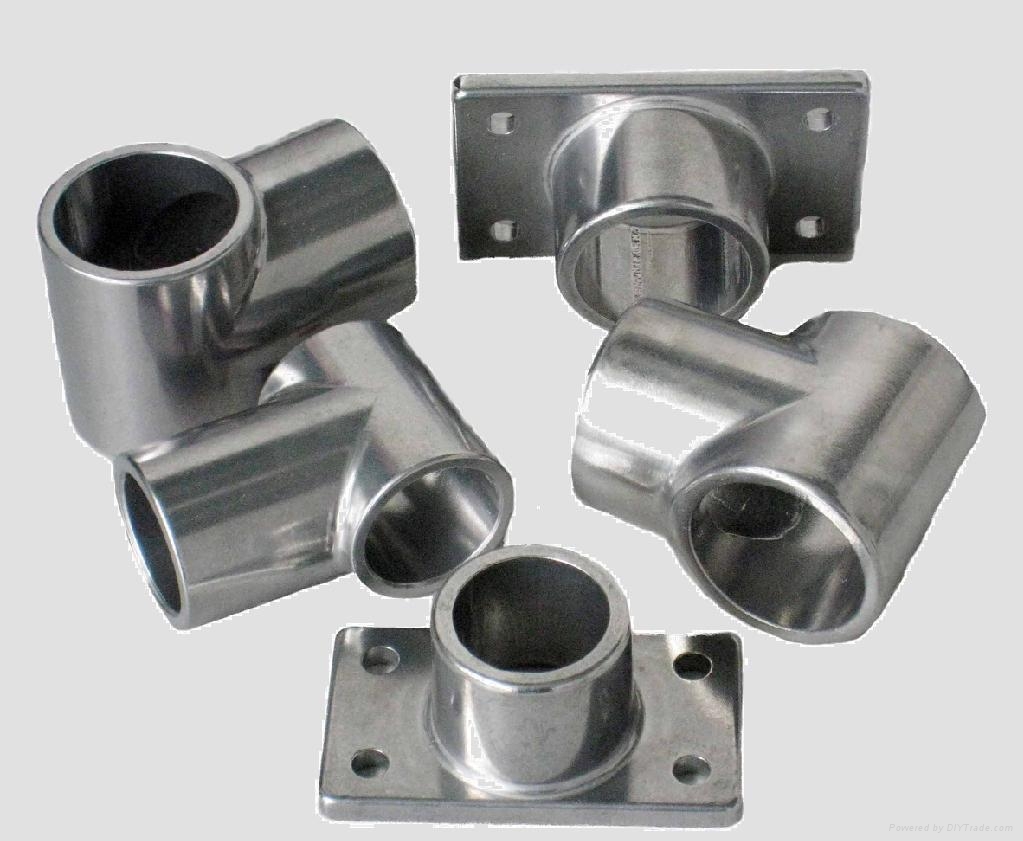